The manufacturing process of machine-made sandwich panels can vary based on the choice of facing and core materials. Different materials have distinct characteristics, properties, and requirements, necessitating adjustments in the manufacturing process to ensure optimal performance and adherence to quality standards. 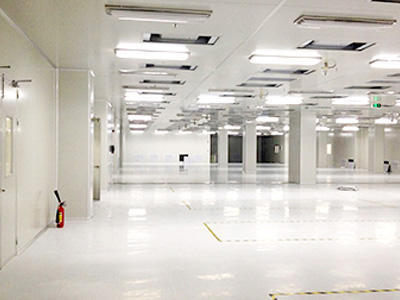
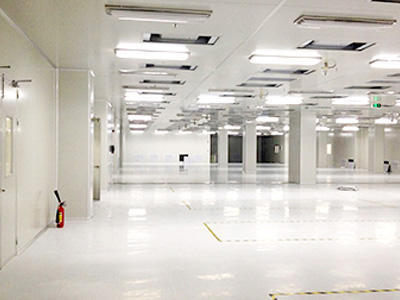
Facing Materials:
Steel: If steel is used as the facing material, the manufacturing process may involve cutting and shaping steel sheets to the desired dimensions. The bonding process must be suitable for steel, and additional steps may be required for treatments such as galvanization or coating for corrosion resistance.
Aluminum: Similar to steel, the manufacturing process for aluminum facing involves shaping the material and may include surface treatments for protection against corrosion. Adhesive selection must be compatible with aluminum.
Fiberglass Reinforced Plastic (FRP): FRP panels may require different cutting and shaping techniques compared to metal facings. The adhesive bonding process must accommodate the unique properties of FRP.
Core Materials:
Polyurethane (PU) or Polyisocyanurate (PIR): The manufacturing process for panels with PU or PIR cores involves injecting or foaming the foam material between the facing layers. Curing processes may involve heat, and the adhesive must be chosen to work effectively with these foam materials.
Expanded Polystyrene (EPS): The process for panels with EPS cores may involve molding or shaping the foam to fit between facing materials. Adhesive compatibility with EPS and the curing process is crucial.
Mineral Wool: Panels with mineral wool cores may involve a different manufacturing process, including cutting and shaping the mineral wool to fit between facing materials. The adhesive must be suitable for bonding to mineral wool.
Adhesive Selection:
Different facing and core materials may require specific adhesives to achieve strong and durable bonds. Adhesives must be selected based on compatibility with the materials, as well as the desired properties of the sandwich panel.
Adhesive curing methods may vary depending on the core material. For instance, some adhesives may cure at room temperature, while others may require thermal curing.
Panel Thickness and Configuration:
The choice of facing and core materials can impact the overall thickness and configuration of the sandwich panel. The manufacturing process may be adjusted to accommodate variations in thickness or specific design requirements.
Additional Treatments or Coatings:
Depending on the facing material chosen, additional treatments or coatings may be applied during or after the manufacturing process. For example, steel or aluminum facings may undergo treatments for corrosion resistance or aesthetic purposes.
Environmental Considerations:
The environmental characteristics of facing and core materials can influence manufacturing processes. For example, materials with high melting points or low resistance to moisture may require specialized handling.
Quality Control Measures:
Quality control measures may be adapted based on the choice of facing and core materials. Testing procedures and criteria for assessing the finished panels may vary.
Regulatory Compliance:
Different materials may be subject to specific regulations or standards. The manufacturing process must align with these requirements to ensure regulatory compliance.