The performance of machine-made sandwich panels in terms of resistance to corrosion, UV exposure, and other environmental factors depends on the specific materials used in the panels, including the facing and core materials, as well as any additional coatings or treatments applied during manufacturing. Here's a general overview of how these panels typically perform:
Corrosion Resistance:
Steel Facing: If the sandwich panel has a steel facing, its resistance to corrosion depends on the type of steel used and any protective coatings applied. Galvanized steel, for example, is more corrosion-resistant due to its zinc coating. The manufacturing process may involve additional treatments or coatings to enhance corrosion resistance.
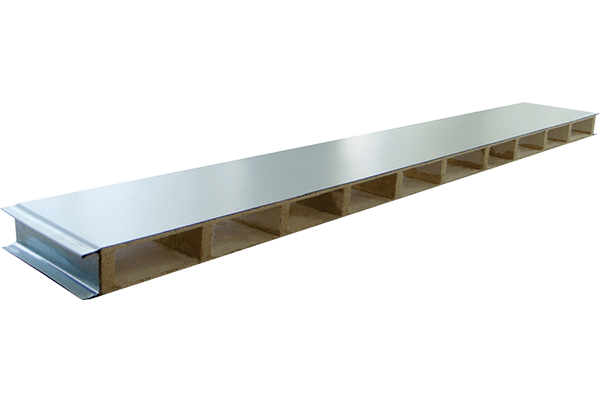
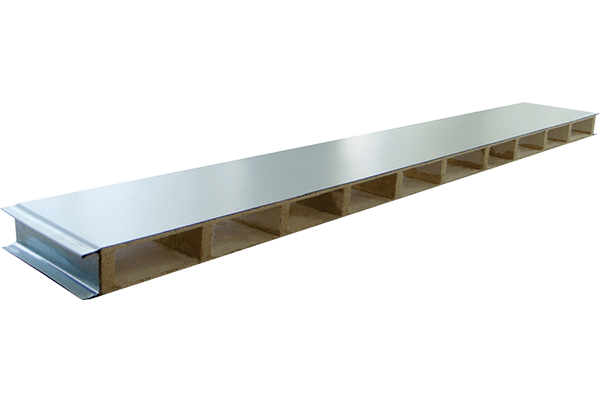
Aluminum Facing: Aluminum panels are naturally resistant to corrosion due to the formation of a protective oxide layer. However, additional treatments or coatings may be applied for enhanced durability in corrosive environments.
FRP Facing: Fiberglass Reinforced Plastic (FRP) panels are inherently corrosion-resistant, making them suitable for environments with high humidity or exposure to chemicals.
UV Exposure:
Steel and Aluminum Facing: While steel and aluminum are durable materials, they can be susceptible to degradation from prolonged exposure to UV radiation. Coatings or finishes may be applied to protect against UV damage. Polyester or fluoropolymer coatings are common for enhancing UV resistance.
FRP Facing: FRP panels generally have good UV resistance, but the specific resin used in the FRP may impact its longevity under prolonged UV exposure. UV-resistant coatings can be applied for additional protection.
Core Materials:
Polyurethane (PU) and Polyisocyanurate (PIR): These foam cores are generally resistant to moisture and do not corrode. However, the facing materials play a crucial role in protecting the core from environmental factors.
Expanded Polystyrene (EPS): EPS cores are resistant to moisture absorption but may have lower resistance to prolonged UV exposure. Adequate facing materials and coatings are essential to protect the EPS core.
Mineral Wool: Mineral wool cores are resistant to moisture and do not corrode. The facing materials and coatings are critical for protecting the core from environmental elements.
Additional Coatings or Treatments:
Depending on the desired level of protection, manufacturers may apply additional coatings or treatments to enhance the panels' resistance to corrosion, UV exposure, and other environmental factors. These may include anti-corrosive primers, sealants, or UV-resistant coatings.
Environmental Considerations:
Humidity and Moisture: The choice of materials and the effectiveness of sealing and coating processes influence the resistance to humidity and moisture.
Temperature Extremes: Sandwich panels can perform well in various temperature conditions. However, facing materials and insulation properties may impact thermal performance.
Chemical Exposure: Resistance to chemicals depends on the specific materials used. FRP facings, for example, may offer better resistance to certain chemicals.