The adhesive bonding process plays a crucial role in the overall efficiency of machine-made sandwich panel manufacturing. The efficiency is influenced by factors such as the bonding technique, curing times, compatibility with materials, and the specific properties of the chosen adhesives. Here's how the adhesive bonding process contributes to efficiency, along with variations in bonding techniques among different types of adhesives:
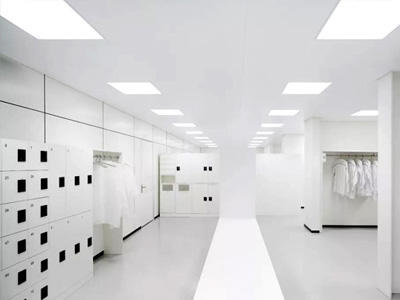
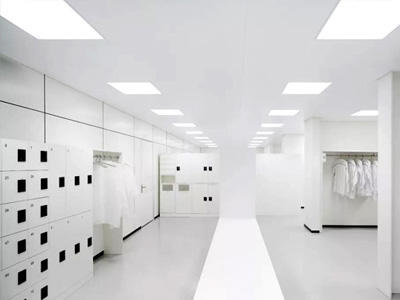
Speed and Automation:
Efficiency Contribution: The adhesive bonding process can be optimized for speed and automation, especially in machine-made manufacturing. Automated processes contribute to faster production, reducing manufacturing times.
Variations: Different adhesives may have varying curing times and requirements. Some adhesives, such as certain epoxy formulations, may allow for rapid curing, contributing to faster bonding processes.
Compatibility with Production Equipment:
Efficiency Contribution: Adhesives are selected based on their compatibility with the specific machinery used in the sandwich panel manufacturing process. This ensures smooth and consistent application, reducing the risk of interruptions or delays.
Variations: Different adhesives may require adjustments in application methods or equipment to ensure optimal bonding. Manufacturers tailor their processes to the characteristics of the chosen adhesive.
Adhesion to Various Materials:
Efficiency Contribution: Adhesives are chosen for their ability to bond to diverse facing and core materials efficiently. This versatility contributes to the production of sandwich panels with a wide range of material combinations.
Variations: Adhesives may have specific affinities for certain materials. The bonding technique may vary to accommodate the compatibility of the adhesive with different facing and core materials.
Curing Methods:
Efficiency Contribution: The curing method of the adhesive influences the speed and efficiency of the bonding process. Some adhesives cure at room temperature, while others may require heat or chemical curing processes.
Variations: Different adhesives may require specific curing conditions. For instance, PU and PIR adhesives often undergo thermal curing, while some epoxy adhesives may require a combination of heat and pressure.
Quality Control and Consistency:
Efficiency Contribution: Adhesive bonding processes can be optimized for quality control, ensuring consistent and reliable bonds across all sandwich panels.
Variations: The type of adhesive used may impact the consistency of the bonding process. Some adhesives may be more forgiving in terms of variations in application conditions.
Environmental Considerations:
Efficiency Contribution: Adhesives that offer reduced cure times or use environmentally friendly formulations contribute to more sustainable manufacturing practices.
Variations: Adhesives with different environmental characteristics may require specific handling or disposal procedures, impacting overall manufacturing efficiency and sustainability.
Handling and Transportation:
Efficiency Contribution: The adhesive bonding process influences the overall handling and transportation of sandwich panels. Properly bonded panels are less likely to experience issues during transit.
Variations: Different adhesives may have varying strengths and resistance to environmental factors, affecting the handling and transportation considerations.
Customization and Adaptability:
Efficiency Contribution: Adhesives that allow for easy customization of sandwich panels, such as the ability to bond diverse materials or create specific designs, contribute to manufacturing flexibility.
Variations: The bonding process may need to be adapted based on the specific requirements of different adhesives, especially if they have unique application characteristics.