Extruded aluminum profiles are widely used in many industries, including the pharmaceutical, biotech, and semiconductor industry. They are usually made from a 6063-T5 alloy and are anodized, which gives them corrosion resistance. They are also lightweight and easy to assemble or disassemble for cleaning, maintenance, or expansion purposes.
In the process of making the extrusions, they are first sheared to a desired length. Then they are mechanically transferred to a cooling table, where they sit until they are room temperature. Once they are cooled to room temperature, the natural twisting that occurred during the shearing process needs to be removed.
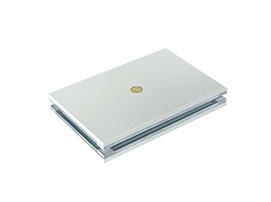
A stretcher is then used to mechanically grip the aluminum channel at either end and pull until it is fully straight and brought into specification. This is a very important step in the production of quality aluminum profiles.
Another critical step in the production of high-performance aluminum extrusions is die bearing. The die bearing is designed to balance the flow of metal in the porthole die and eliminate extrusion defects.
The die bearing is a critical component in the production of large aluminum profiles with high length-width ratio and small cavities. A good die bearing allocates the material reasonably in porthole die and improves considerably the uniformity of metal flow velocity distribution at the exit of die, thereby improving the performance of the extrusion process.
In addition, the die bearing is an effective means for balancing the flow of metal in porthole die and preventing defects such as pin-point. In particular, a long die bearing increases additional frictional resistance in the zone with higher velocity, resulting in a decrease in exit velocity. In contrast, a short die bearing reduces fictional resistance in this zone, resulting in a greater exit velocity.