Choosing the right core and facing materials for the production of handmade sandwich panels is crucial to achieving the desired performance and characteristics for your specific project. The selection process involves considering factors like strength, insulation, weight, and environmental conditions. Here are steps to help you choose core and facing materials:
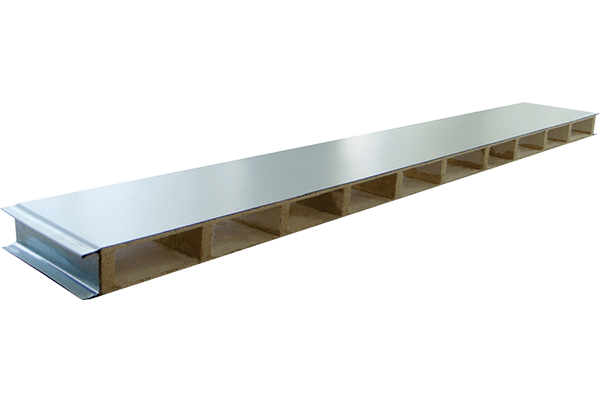
1. Determine Project Requirements:
Start by clearly defining the requirements of your project. Consider factors such as load-bearing capacity, insulation properties, environmental exposure, and any specific industry or regulatory standards.
2. Core Material Selection:
Foam Core: Foam cores, such as expanded polystyrene (EPS) or polyurethane foam, are lightweight and offer excellent insulation properties. They are commonly used in applications where thermal or sound insulation is important.
Plywood Core: Plywood cores are sturdy and provide structural strength. They are suitable for applications requiring a strong and rigid panel, such as subfloors, roofing, or vehicle paneling.
Honeycomb Core: Honeycomb cores consist of hexagonal cells that offer high strength-to-weight ratios. They are often used in aerospace and marine applications where lightweight yet robust panels are required.
Balsa Wood Core: Balsa wood cores are lightweight and provide good insulation properties. They are used in applications like model aircraft and lightweight boat construction.
Nomex Core: Nomex honeycomb cores are lightweight and have excellent fire-resistant properties. They are used in applications where fire safety is a concern.
Aluminum Core: Aluminum cores offer durability and stiffness. They are used in applications requiring high strength and resistance to corrosion.
Cork Core: Cork cores provide natural insulation and are eco-friendly. They are used in applications like bulletin boards and interior wall panels.
3. Facing Material Selection:
Plywood Facing: Plywood facing provides strength and durability. It is commonly used in construction and structural applications.
Fiberglass Facing: Fiberglass facing offers resistance to corrosion and is often used in marine or outdoor applications.
Aluminum Facing: Aluminum facing provides a lightweight yet strong surface. It is used in aerospace and automotive applications.
Steel Facing: Steel facing offers high strength and is used in applications requiring heavy-duty protection.
Plastic or PVC Facing: Plastic or PVC facings are lightweight and corrosion-resistant. They are suitable for indoor applications.
Wood Veneer Facing: Wood veneer facings provide an attractive finish and are used in furniture and interior design projects.
Composite Facing: Composite facings combine materials like fiberglass and resin for added strength and durability.
4. Consider Budget: Assess the budget available for your project, as some materials may be more cost-effective than others.
5. Environmental Factors: Consider whether the handmade sandwich panels will be exposed to outdoor elements, moisture, UV radiation, or extreme temperatures, as this will impact material choices.
6. Weight Restrictions: If your project has weight restrictions, opt for lightweight core and facing materials.
7. Test and Sample: Whenever possible, obtain samples or test materials to assess their suitability for your project before proceeding with production.