The handmade sandwich panel is a type of laminate that consists of two relatively stiff face sheets that are separated by a lightweight core material. They offer a combination of high rigidity and low weight which is especially useful for the transport industry, where mass reduction is essential.
The main function of the core material is to stabilize the facings and carry most of the shear loads through the thickness of the panel. Typically, the core is made from either a metallic honeycomb or lattice structure.
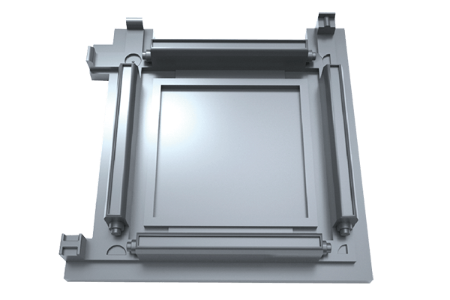
In addition, there are a few other materials that can be used as the core of the sandwich panel, including balsa wood and fiberglass. These are much lighter than traditional particleboard or fiberboard, and are therefore a great choice for the sandwich panel market.
Increased Core Density and Number of Layers.The number of layers within the face sheets improves the flexural and shear performance of a sandwich panel because the thicker the laminate, the more resistive it is to the load. This means that at higher loads, the core will absorb more energy and the deflection of the sandwich panel will decrease.
In addition to providing the structural strength of the sandwich panel, the core is also an effective insulator. This helps reduce heating and cooling costs in the building. In fact, it can be a major factor in reducing the overall cost of the project.